Production process in our factory runs in the following plants:
- plant for material cutting and plastic deformation
- hand work plant (metal works and welding works)
- machining plant (light and heavy)
- mechanical and electro installation plant
- anti-corrosion protection (ACP)
- heat treatment plant
Material cutting and plastic deformation plant is equipped with :
- cutting saws for pipes and sections cutting
- hydraulic scissors for sheet metal cutting
- motor cutters for gas cutting
- two portal CNC sheet metal cutters by using gas and plasma
- sheet metal cutting laser
- hydraulic press SCHAFFER of 2000t
- bending machine with 4 rollers
- two small hydraulic presses
- hydraulic press brake of 600t (hydraulic press for angled bend)
VARCUT 6,5R.P2 / B10-5.0×20,0 / (1Pl+1G) + 1G
- Producer: Varstroj (Slovenia)
- CNC control: YES
- Number of cutting heads: 2
- Number of burners: 3 (2 x gas, 1 x plasma)
- Working width: 5.000 mm
- Working length: 20.000 mm
- Maximum gas cutting depth: 300 mm
- Maximum plasma cutting depth: 30 mm
- Load of crane serving the machine: 20.000 kg
Hydraulic press brake PSH 600 / 6000
- Producer: Jelšingrad (Republic of Srpska)
- Pressing force: 6.000 kN
- Working length: 6.000 mm
- Sides stand interspace: 5.050 mm
- Maximum upper die beam stroke: 300 mm
- Table and rocker interspace adjustment range: 220 mm
- Table and toolholder maximum interspace: 600 mm
- Table width: 300 mm
- Working speed: 7,5 mm/s
- Load of crane serving the machine: 20.000 kg
Plant for material cutting and plastic deformation
also has a 2.000 t press and a sheet metal straightening and rolling machine. These two machines make Montavar Metalna Lola d.o.o. a leader in the former South-East Europe countries, as regards preparation followed by manufacture of major items that are used in hydro and thermal energy plants, and also in the plants using recoverable energy sources (wind generators, etc.).
Hydraulic press
- Producer: SCHAFFER
- Maximum thickness of material: 5800 mm
- Working table length: 7.200 mm
- Maximum pressing force: 18.000 kN
- Maximum upper die beam stroke: 800 mm
- Table and holder maximum interspace: 1.200 mm
- Table and holder minimum interspace: 400 mm
- Table with: 800 mm
- Load of crane serving the machine: 30.000 kg
Bending machine with 4 rollers
- Producer: SCHAFFER-METALNA
- Maximum thickness of material: 4000mm
- Upper roller diameter: 860mm
- Bottom roller diameter: 860mm
- Side roller diameter 720mm
- Optimum pipe diameter range: .1000 mm – .3000 mm
- Optimum table width for material thickness 30 – 80 mm: 2m
- Maxim. thickness of bent material 180 mm for table thickness 0,8m
- Roller speed: 2-10 m/min
- Load of crane serving the machine: 30.000 kg
Hand work plant
It is intended for metal and welding works and has a large number of:
- REL welding machines TIG
- MIG/MAG welding machines
- automated welding machine
- special tools

Machining plant
consists of the segments of light and heavy machining
Light machining consists mainly of:
- universal milling machine
- grinding machines
- boring machines
- milling machines
- gear cutting machines
The basis of heavy machining consists of:
- portal milling machines
- double column vertical lathes
- horizontal boring/milling machines
- portal grinding machines
- portal shaping machines
- coordinate and radial boring machines
- deep boring machine.
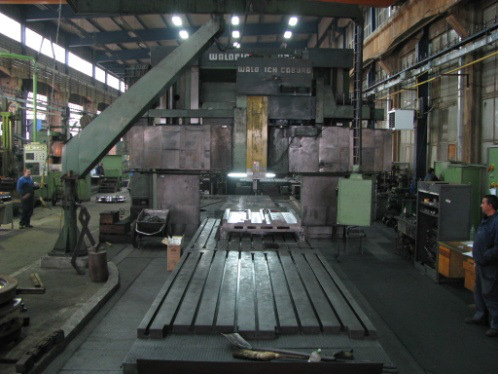
Portal milling machine PG 240
- Producer: Waldrich Coburg (Germany)
- CNC control: Sinumeric 820 CNC Siemens
- Spindle speed: 600 rev/min
- Spindle diameter: 220 mm
- Table size: 2.400 x 8.500 mm
- Workpiece width: 2.600 mm
- Workpiece height: 2.000 mm
- Machine travels: X=9.000 mm, Y=3.500 mm, Z=1.000 mm, W=2.000 mm
- Load of crane serving the machine: 20.000 kg
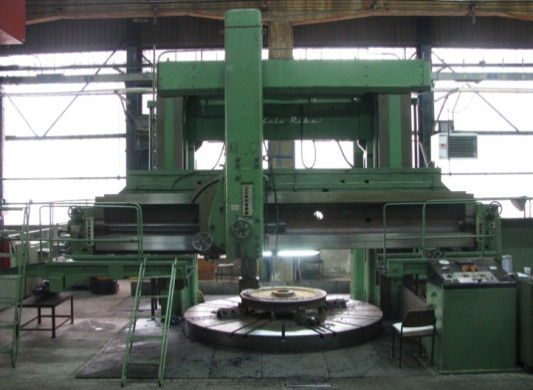
Double column vertical lathe DK 3300
- Producer: Ivo Lola Ribar (Serbia)
- Table speed: 46 rev/min
- Table diameter: 3.000 mm
- Workpiece turning diameter: 3.300 mm
- Workpiece height: 2.000 mm
- Workpiece weight: 60.000 kg
- Machine travels: X=1.750 mm, Z=1.200 mm, W=2.000 mm,
- Load of crane serving the machine: 20.000 kg
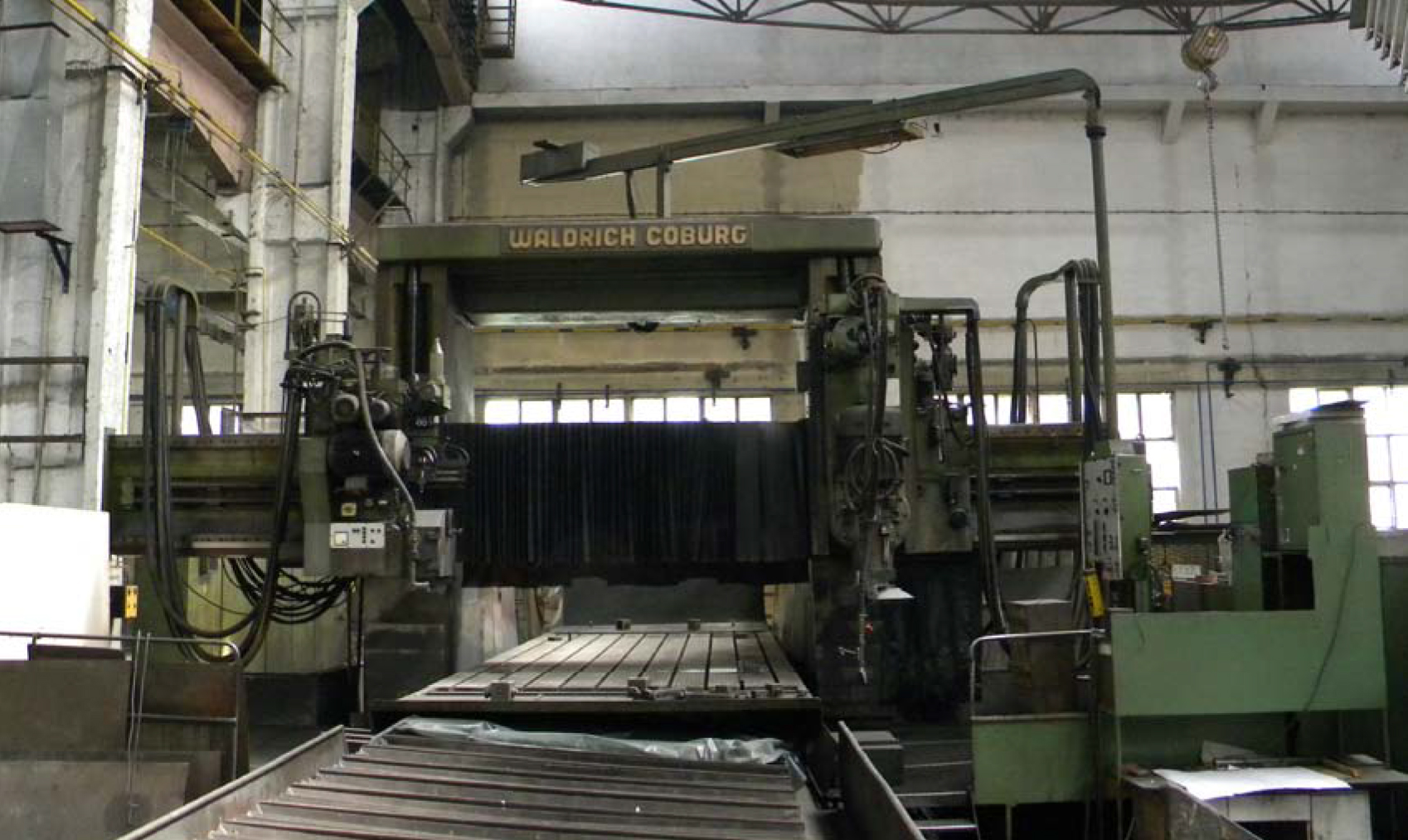
Portal grinding machine
- Producer: Waldrich Coburg (Germany)
- Table size: 2.500 x 6.000 mm
- Workpiece width: 2.800 mm
- Workpiece height: 2.000 mm
- Workpiece weight: 23.500 kg
- Machine travels: X=6.700 mm, Y=2.800 mm, Z=700 mm, W=2.000 mm
- Load of crane serving the machine: 20.000 kg
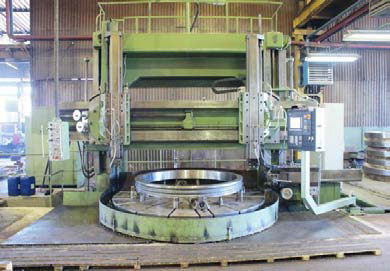
Double column vertical lathe CNC
- Maximum diameter: 3200 mm
- Minimum diameter: 400 mm
- Load of crane serving the machine: 20.000 kg
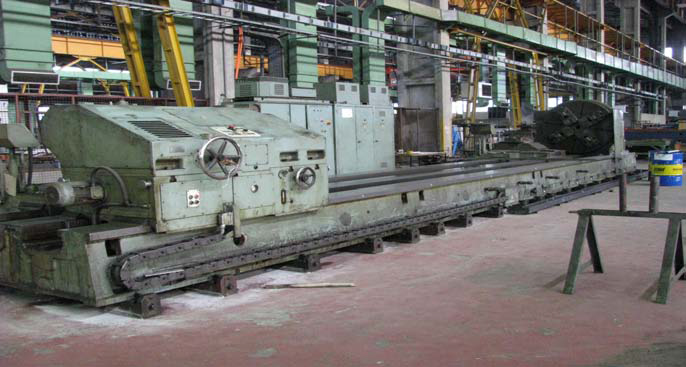
Lathe 1A 665N267
- Producer: CCCP
- Workpiece turning diameter: 1.400 mm
- Machine travels: 10000 mm,
- Load of crane serving the machine: 30.000 kg

Horizontal boring/milling machine
- Producer: Ivo Lola Ribar (Serbia)
- Table speed: 1000 rev/min
- Table size: 1500×1700 mm
- Workpiece weight: 6.000 kg
- Machine travels: X=4.000 mm, Y=2.500 mm
- Load of crane serving the machine: 20.000 kg
- Lathe
- Maximum turning diameter: 1200 mm
- Maximum workpiece length: 8000 mm
Gear cutting machine, cylindrical, straight- and bevel-toothed
- External gears diameter: 3600 mm
- Module: 40
- Internal gears: Dmax=3000 mm
- Module: 30: 500 mm
Gear cutting machine, conical, disk pairs with helical gears
Klingelnberg
- Maximum diameter: 1100 mm
- Maximum module: 21,5mm
Gleason
- Maximum diameter: 457 mm
Machine for machining of splined shaft and worm gears



Operations in the mechanical and electro installation plant :
- Installation of machine tools
- Installation of welded structure assemblies (test installation)
- Final inspection before delivery
- Packing of product for delivery to the end user

Processes in the anti-corrosion protection plant (ACP):
- sandblasting
- painting
Sandblasting is carried out by steel shots. Granule size is in accordance with the client’s requirements, i.e. with the desired surface roughness.
We sandblast sheet metal of 4mm thickness and obtain 2nd and 3rd surface quality. Shot collecting and transport system is automated.
Sandblasting is manual. In the paint shop, we apply all protection systems.

Induction welding:
- Gear diameter 4000mm, gear module 10-40
- Axis diameter 300 x 2000mm
- Wheel diameter 4000mm
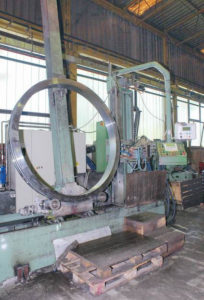
Processes in the heat treatment plant:
- improving
- cementing
- phosphating
